Latest Industry News Briefs Courtesy of PMTA
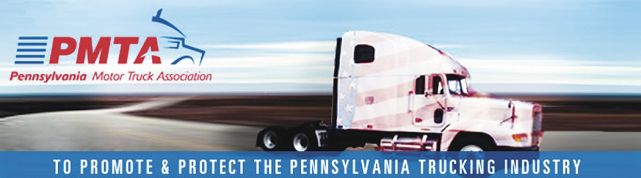
ATA Pleased to See Biden Administration Recognize the Need for Improved Truck Parking
The American Trucking Associations President and CEO Chris Spear made the following statement after the Department of Transportation highlighted the need for improved truck parking in its Supply Chain Assessment of the Transportation Industrial Base: Freight and Logistics report:
“ATA is pleased to see the Department of Transportation and the Biden Administration have recognized that addressing the shortage of truck parking is a critical need. The report acknowledges what ATA and truck drivers have been saying for years: the lack of safe truck parking negatively impacts our tangled supply chain, and more importantly, it makes an already difficult job far more challenging.
“The scarcity of truck parking spaces across the country decreases safety for all highway users, exacerbates the industry’s longstanding workforce challenges, contributes negatively to driver health and well-being, diminishes trucking productivity, and results in unnecessary greenhouse gas emissions.
“We welcome President Biden’s and Secretary Buttigieg’s support for expanding truck parking capacity throughout the supply chain. We hope that DOT will use the historic increase in grant money in the Infrastructure Investment and Jobs Act to invest in projects that address this critical, growing and long-neglected obstacle to the safe and efficient delivery of the 72 percent of domestic freight that is moved by truck drivers.”
ATA Reacts to Biden Administration’s Heavy-Duty Truck Emissions Proposal
Arlington, VA… The American Trucking Associations President and CEO Chris Spear said the association and industry would be closely reviewing the Biden Administration’s proposed emissions rules for heavy-duty trucks, but that it will be critical that these rules result in usable, reliable and cost-effective equipment:
“We share the Biden Administration’s goals of reducing air pollution – as a longtime member of EPA SmartWay Transport Partnership – we have worked in harmony with environmental regulators to successfully reduce greenhouse gas and NOx emissions.
“We will be looking very closely at the proposal put forth today by the administration, and working with them to shape an outcome that builds on those reductions, while not hurting the reliability of the trucks and trailers we purchase, nor imposing unreasonable or unworkable costs on our industry.
“We want to ensure that the Biden Administration sets one, single national NOx emissions standard and that such standard can be achieved with workable, reliable technology – anything less than that will be extremely problematic for ATA and our members.”
ATA Thanks NTTC For Pledge to Help Fight Rhode Island Toll Scheme
Arlington, VA… The American Trucking Associations leaders thanked the National Tank Truck Carriers for their contribution of $50,000 to the industry’s ongoing challenge to Rhode Island’s extortionary truck-only tolls scheme.
“Winning this suit is critical for trucking” said ATA President and CEO Chris Spear, “If this exorbitant, predatory tolling plan is allowed to stand, it will be replicated across the country. This is an all-hands on deck situation, so we are grateful for NTTC’s support in this crucial fight.”
ATA, through the ATA Litigation Center, and a number of carriers based in New England, sued Rhode Island over its RhodeWorks tolling program that specifically targets the trucking industry. The industry’s challenge is currently being weighed in the U.S. Court of Appeals for the First Circuit.
“We appreciate NTTC stepping up to help in this effort. Their support is critical to our success in this suit,” said ATA Chairman Harold Sumerford Jr., CEO of J&M Tank Lines. “And as an NTTC member and a past chairman, I want to thank them personally for their leadership in making this a priority for their members and our industry.”
“Hearing what the consequences of losing this suit would be for our industry, deciding to help was a no-brainer,” said NTTC President and CEO Ryan Streblow. “We are proud to stand with ATA on behalf of our industry to stop Rhode Island, or any state, from targeting trucking with these kinds of predatory schemes.”
NTTC leadership made its $50,000 commitment to the Rhode Island litigation effort at the association’s annual board meeting in Palm Beach Gardens, Florida.
Centerline Drivers Names Patty Burns Respect the Drive Driver of the Year
SANTA ANA, CA… Centerline Drivers awarded Patty Burns its inaugural Driver of the Year award. This is the first year Centerline Drivers has awarded the honor as part of its Respect the Drive program, which celebrates the incredible work truck drivers do every day.
Burns, of Concord, Calif., has driven more than 1 million in her 11 years with Centerline and more than 2 million miles since she started driving in 1999. She was chosen from more than 500 drivers based on a perfect safety record, attendance and work with Centerline’s customers. She drives for Toyota, who consistently praise her ability to get the job done and her positive attitude.
“I have always taken great pride in being a truck driver,” said Burns, who has been driving since 1999. “I feel like I am an ambassador for the industry and for women in trucking. I always focus on being the best driver I can be. I have a passion for the industry and I really enjoy the partnerships with my customers.”
The award comes with a plaque, Respect the Drive gear, a monetary bonus and recognition from both Centerline and Toyota.
“Patty Burns exhibits exemplary driving skills as shown by her excellent safety record,” said David Gadberry of Toyota Quality Parts Express. “Patty consistently reports for her runs on time. She performs her work expediently and efficiently, offering high value to our line haul operations. Patty always documents her work, communicates clearly and effectively and is willing to learn new tasks.”
Randy Beulah and Ronald Pettiford earned runner-up stats and will also receive Respect the Drive Gear.
“Patty is not just our Driver of the Year, she is a pioneer for women in the trucking industry,” said Centerline Drivers President Jill Quinn. “It is incredible that she has driven more than 2 million miles, all while being the safest driver on the road and building great relationships with our customers. She is the epitome of what a driver should be and I’m thrilled to present her with this honor.”
Throughout 2022, Centerline will continue to encourage people to Respect the Drive by illustrating the positive things truck drivers do every day and celebrating our drivers and the industry.
Masks Optional For Oregon DMV Customers As Of March 14
SALEM , OR… Masks are now optional for customers indoors at Oregon DMV offices and inside cars during DMV drive tests as of Monday, March 14.
.
“As a reminder, masks are still required for both DMV employees and customers inside DMV offices and on drive tests through Friday, March 11,” DMV Administrator Amy Joyce said. “Even after the mask requirement ends, you will still see customers and employees wearing masks by their own choice in DMV offices.”
DMV offices are open for walk-in service or by appointment. However, staff shortages or winter weather occasionally force an office to close for a day or more. Before you visit a DMV office, see if you can get the DMV service you need at DMV2U.Oregon.gov or make sure your local office is open by checking at OregonDMV.com.
“When you visit an office, please continue to be patient and courteous with other customers and our staff, and help us get Oregonians what they need as smoothly as we can,” Joyce said. “DMV offices are almost always busy because of the pandemic and staffing shortages, and we get busier during the summer – and as we get closer to the May 2023 Real ID requirement at airports.”
DMV and other state agencies follow the guidelines of the Oregon Health Authority in setting COVID-19 safety requirements. DMV also sped up deployment of new online services so that many customers could get the services they need from home.
“We will always encourage people to use DMV2U for convenience. Many of our services, including replacing plates, renewing your vehicle registration, and changing your address can be done without ever needing to come to a DMV office. You can also schedule your own behind-the-wheel drive test appointment using DMV2U,” Joyce said.
Oregon DMV partners that are private businesses – such as drive test providers, driving schools and teen driver education – may choose to continue mask requirements under their own business rules after March 11.
Get ready for air travel now
If you travel by air or might in the future, make sure you have identification acceptable at airport security checkpoints. Starting in May 2023, you will need a Real ID-compliant form of ID for all flights such as a Real ID-compliant driver license, a passport, passport card or U.S. military ID.
Don’t wait until the rush for Real ID licenses and passports! If you want the Real ID option on your Oregon driver license or ID card, you must apply in person – walk in or by appointment.
To make sure you have all you need for Real ID, create your own checklist of documents you’ll need to bring to DMV with our online tool at Oregon.gov/RealID.
Trucking Industry: Increase Domestic Energy Production Now
Arlington, VA… The American Trucking Associations is calling on the Biden Administration to take immediate steps to boost domestic energy production. In a letter sent on March 10th to the White House, ATA outlined specific actions the U.S. can take to provide relief at the pump for motor carriers and motorists across the country.
Fuel is the second largest operating expense for trucking fleets, and surging diesel prices threaten to decimate trucking capacity at a time when the supply chain is already under extreme stress.
The text of the letter follows:
Dear Mr. President:
The trucking industry is the backbone of the American economy, moving 73 percent of our nation’s freight, or 10 billion tons of goods annually. Our ability to do so on a cost-efficient basis for our customers throughout the supply chain depends on certain economic conditions, including fuel prices, which are typically a fleet’s second highest operating expense. Right now, escalating fuel prices are driving up the transportation cost of all goods, adding yet another layer of inflationary pressure on every sector throughout the entire economy.
The impact is particularly hard on the 97 percent of motor carriers that operate 20 trucks or fewer and are designated as small businesses. These fleets do not operate at a scale necessary to negotiate lower fuel prices or to offset costs from shippers. Lacking the financial reserves to weather this storm, many of these companies are at risk of failing given current projections for global crude prices over the next 12 months. This would decimate U.S. trucking capacity, unleashing catastrophic consequences for a supply chain that’s already overstressed.
The American Trucking Associations therefore urges the Biden Administration to increase American oil and natural gas production to help bring down domestic fuel prices, providing immediate relief to our nation’s supply lines. We cannot let an energy crisis compound the supply chain crisis, and we have the power and resources to prevent that from happening. Specifically, ATA calls on the Administration to:
* Expedite onshore and offshore oil and natural gas permitting to spur expanded production;
* Initiate immediate lease sales in current production areas in the Central and Western Gulf of Mexico;
* Encourage expedited carbon capture & sequestration rulemaking to ensure that America remains the world’s leader in carbon reduction technology development;
* Work with both domestic and international oil and natural gas producing nations to help reduce global oil prices; and
* Consider timed releases from the Strategic Petroleum Reserve.
In 2019, commercial trucks consumed 46 billion gallons of diesel and gasoline. Motor carriers spent $112 billion on diesel fuel that year, when the annual cost of diesel ranged between $2.97 and $3.17 per gallon. This week, the U.S. Department of Energy reported the national average diesel fuel price at $4.85 per gallon as of March 7—the highest price in U.S. history. Diesel fuel prices on the West Coast are extraordinarily high, with an average price of $5.76 per gallon in California.
More than half the cost of a gallon of diesel fuel is attributed to the price of crude. Crude prices are now well over $100 per barrel, with forecasters predicting $185 per barrel by year’s end. These trend lines are not sustainable for the trucking industry and signal a major warning for the supply chain.
We cannot afford to ignore our nation’s current energy needs in a fog of partisan idealism about the future of energy use. The trucking industry supports an all-of-the-above approach when it comes to securing our energy future. But the transition to cleaner and renewable fuels over the horizon requires a practical, actionable bridge in the here-and-now, beginning with the abundant sources readily available at home.
Taken together and immediately, the actions outlined above would bring immediate relief at the pump for America’s truckers and all motorists. ATA stands ready to assist you in keeping our economy and nation united, connected and strong.
Most respectfully,
Chris Spear
ATA, IMCC Pleased by Biden Administration’s Action Against Foreign Ocean Lines
Arlington, VA… The American Trucking Associations and the ATA Intermodal Motor Carriers Conference expressed their appreciation to President Biden and his administration for highlighting the unscrupulous business practices of a monopoly of foreign-owned ocean shipping lines in last night’s State of the Union Address.
“We are pleased that the Biden Administration is taking long overdue steps to limit the power of the ocean shipping cartel to hurt American businesses and consumers,” said IMCC Director Jonathan Eisen. “ATA and IMCC have long been fighting against the predatory practices of these foreign-owned companies and we appreciate President Biden shining a light on this critical issue.”
In his address, President Biden noted that exorbitant rate increases by this monopoly of overseas companies, especially during the pandemic, have been a driver of inflation.
“When corporations don’t have to compete, their profits go up, your prices go up, and small businesses and family farmers and ranchers go under. We see it happening with ocean carriers moving goods in and out of America,” he said. “During the pandemic, these foreign-owned companies raised prices by as much as 1,000% and made record profits. Tonight, I’m announcing a crackdown on these companies overcharging American businesses and consumers.”
Price hikes by these companies have generated more $150 billion in profit at the expense of American truckers, other businesses and consumers. ATA and IMMC are suing these profiteers, and that legal action is pending before the Federal Maritime Commission.
ATA’S Spear: Time for Washington to Get Real About American Energy Independence
Arlington, VA… American Trucking Associations President and CEO Chris Spear recently issued the following statement:
"With fuel prices skyrocketing, and hardworking Americans feeling the intensifying pain at the pump, it is time the Biden Administration and Congress get real about American energy independence.
“The horrific war in Ukraine makes crystal clear why we need to increase domestic energy production, and must eliminate energy reliance on nations that pose a threat to our national and economic security. The millions of Americans who keep our country moving forward should not be put in the position of having to spend a single dollar on Russian fuel that lines the war chest of a genocidal tyrant.
"Our addiction to foreign energy sources not only empowers America's most dangerous adversaries, but it's also having a serious impact right now on our industry's ability to keep costs down for our customers throughout the supply chain. The trucking industry calls on the President and Congress to take immediate, concrete steps to increase domestic production and restart critical pipeline projects in the face of this clear and present danger.
“We cannot afford to ignore our nation’s current energy needs in a fog of partisan idealism about the future of energy use. The trucking industry supports an all-of-the-above approach when it comes to securing our energy future. But the transition to cleaner and renewable fuels over the horizon requires a practical, common-sense bridge in the here-and-now, beginning with the abundant sources readily available here at home."
Bendix Shrinks Its Carbon Footprint Further In 2021 With New Solar Array, Reduced Energy Use, And Continued Zero-Waste Wins
AVON, OH… Bendix Commercial Vehicle Systems LLC (Bendix) continued to reach new sustainability milestones in 2021 in support of its larger environmental goals to reduce energy consumption; divert waste from landfill; and increase its use of green, renewable energy.
By the end of 2021, the company had reduced its energy consumption by more than 16 million kilowatt-hours over the most recent seven-year period. And for the second year in a row, the company diverted 99.9% of its waste from landfill, with less than 10 tons of material from all Bendix locations combined being sent to landfill. The amount represented a decrease of 37% from the 16 tons of material landfilled in 2020 and a 98% reduction from the 508 tons landfilled in 2019. The remaining 14,703 tons of excess or spent materials were either diverted, recycled, or reused.
On the zero-waste front, seven Bendix manufacturing locations – plus the former Elyria, Ohio, corporate headquarters – achieved the company’s official Zero Waste to Landfill Certification in 2021 for the second year in a row.
And in terms of renewable energy use, Bendix achieved a key element of its overall climate strategy with the August startup of the company’s first solar array, a 1.168-megawatt installation at its operation in Huntington, Indiana. The array, featuring 2,612 solar panels, can supply enough power to satisfy about 30% of the energy needs at the primary manufacturing facility on the Huntington campus. It’s also estimated to save approximately $140,000 in energy costs and lead to a 3% decrease in Bendix’s overall carbon footprint across North America.
“2021 was another outstanding year for the Bendix sustainability strategy, as the company continued progressing toward our overarching climate action goals and our key sustainability milestones,” said Maria Gutierrez, Bendix director of corporate responsibility and sustainability. “Despite the work and environmental challenges brought by the second year of the pandemic, Bendix team members continued to do their part to reduce waste, increase energy efficiency, and reduce the company’s carbon footprint across North America. And together, these efforts resulted in ongoing decreases in energy consumption and landfill wastes, alongside gains in renewable energy use and waste diversion. All of these successes deserve to be celebrated and recognized.”
Bendix is the North American leader in the design, development, and manufacture of active safety, air management, and braking solutions for commercial vehicles. It is also a member of Munich, Germany-based Knorr-Bremse, the global market leader for braking systems and a leading supplier of other safety-critical rail and commercial vehicle systems.
Together, the two organizations are focused on achieving reduced energy use, increased waste diversion, and improved energy efficiency in support of their deep alignment and ongoing support of the United Nations’ (U.N.) ambitious Sustainable Development Goals (SDGs). These 17 overarching environmental objectives adopted by U.N. member states promote prosperity while protecting the environment. Two of the objectives – Responsible Consumption and Production (encompassed within SDG 12) and Climate Action (the focus of SDG 13) – are central to Bendix’s sustainability efforts.
Achieving Zero Waste to Landfill for the Second Year in a Row
During 2021, Bendix secured a major sustainability win by once again achieving the company’s zero-waste-to-landfill objective at eight Bendix manufacturing sites within the network of manufacturing campuses, as well as the former corporate headquarters in Elyria. And in April 2021, the company’s Zero Waste to Landfill Certification program was recognized with a Best Practice Award from the U.S. Department of Energy.
As of late October 2020, the Elyria facility and all but two Bendix manufacturing sites and the recently acquired sites of R.H. Sheppard Co., Inc. had achieved the company’s Zero Waste to Landfill Certification. The program centers around a detailed self-certification process, whereby each location must meet eight major requirements related to waste management, waste diversion, and continuous improvement to verify that the site is diverting 100% of its waste from being landfilled.
“Our sites achieve our Zero Waste Certification by consistently diverting 100% of both industrial and nonindustrial wastes from landfill – using recovery, recycling, composting, or another diversion method or technology, including waste-to-energy,” said Bill Schubert, Bendix corporate manager, environmental and sustainability. “We’ve set up a hierarchy across locations that focuses first on eliminating wastes, before applying methods to reduce, reuse, recycle, and reclaim them. If and when these strategies are not available, sites then have the option to utilize waste-to-energy (WTE) technologies or incineration to manage wastes.”
In achieving the Zero Waste Certification, each location also uses a combination of multiple technologies, processes, and cultural changes in place across Bendix to drive reduction or elimination of wastes. These include the company’s Sustainable Food Service Policy, which eliminates plastic water bottles and Styrofoam products; launching new processes, such as centralized waste collection and spent material audits (aka dumpster dives); and utilizing new or innovative technologies, such as WTE technologies, a composting program, and the use of food waste digesters.
For example, the Acuña, Mexico, manufacturing campus implemented food waste digesters at cafeterias in three of its plants in late 2019. In 2021, their second year of operation, these food waste digesters helped divert 50 tons of food waste from being landfilled.
The company credits its strong Environmental Management System and corporate values as key contributors in developing and achieving the zero-waste program. Begun in 2010, Bendix’s evolving waste management process and ISO 14001 certifications have helped provide the framework for continuous improvement.
Continued Green Outreach Efforts
Companywide efforts hosted by Bendix’s Green Teams also helped to raise awareness of and employee participation in Bendix’s 2021 sustainability programs. Throughout the pandemic, these employee-led teams, charged with identifying or coordinating green projects, continued to sponsor activities to help increase awareness both on and off the job.
As in 2020, Bendix’s Green Teams helped sponsor and lead litter cleanup campaigns during 2021. The first campaign was kicked off to align with April’s Earth Day and focused on the North American Bendix locations. Team members worked together with family members to help exceed a 5,000-piece target by cleaning up more than 5,800 pieces of litter.
Building on the success of this program, Bendix expanded the initiative later in the year to Knorr-Bremse locations globally and established an ambitious 50,000-piece goal. A total of 839 Bendix and Knorr-Bremse colleagues around the world rose to the challenge, resulting in over 102,000 pieces of litter picked up in the communities where company employees live and work.
The Successful Launch of Solar Power
Among the most significant sustainability achievements for Bendix during 2021 was the August completion and startup of the new 1.168-megawatt solar array in Huntington. Bendix’s first solar energy installation, the array satisfies about 30% of the energy needs at Huntington Plant 1, a massive manufacturing plant on the campus.
Indianapolis-based PSG Energy Group managed construction of the array, which when completed was the largest on-site solar installation in Huntington County. At full capacity, the solar project produces 1.5 million kilowatt-hours of electricity, delivering an estimated $140,000 in annual electric utility savings.
With the installation, Bendix expects to reduce its greenhouse gas emissions in line with its long-term sustainability goals. Key among them is the 2020 commitment by Bendix and parent company Knorr-Bremse to cut CO2 emissions in half by 2030. Additionally, in 2021, Knorr-Bremse ramped up efforts to achieve carbon neutrality by maximizing renewable energy purchases and offsetting energy use. Toward that end, over the past two years, the company has significantly exceeded its climate target of reducing CO2 emissions by 4.2% each year.
The Huntington solar array will contribute to that success, as it’s expected to provide a 19% reduction in the campus’ carbon footprint and a 3% reduction in Bendix’s carbon footprint across North America.
The solar array produces electricity through 2,612 450-watt panels. During the plant’s normal hours of operation, all of the energy generated is used by the facility. During nonworking hours like weekends and holidays, however, Bendix can send excess energy back to the electrical grid, increasing the utility’s green energy and reducing Bendix’s utility costs.
The next sustainability milestone for Bendix is the installation of two solar arrays at the Acuña, Mexico, manufacturing campus – each generating 1,000 megawatt-hours of electricity annually and reducing by 13% the campus CO2 emissions from the 2018 baseline. This project was approved in 2021 and is on track to be completed in mid-2022.
The company plans to achieve a 50% reduction in carbon emissions by 2030. Bendix will do this through continued energy efficiency projects, the installation of on-site renewable energy, and by procuring green energy in the marke
“With decreases in energy consumption and landfill waste, and an increase in our use of green energy, such as with the Huntington solar array, we’ve come a long way in 2021,” Gutierrez said. “We’re also very proud of the ways we’ve addressed challenging waste streams and have continued to improve energy efficiency throughout 2021. These rewarding accomplishments are helping to keep us ahead of schedule when it comes to achieving our long-term climate, waste, and energy goals. Everything we’ve accomplished so far is proof that our strategy is sound and effective.”
CTA Expresses Concern with Government Moving Goalposts on ELD Enforcement
TORONTO, ONTARIO… The Canadian Council of Motor Transport Administrators (CCMTA) is announcing a delay in enforcement of the ELD mandate from June 2022 to January 2023.
The Canadian Trucking Alliance (CTA) is very disappointed by this announcement and has reasonable doubts that the new January date is certain, from a national perspective, based on the lack of legislative preparedness of four jurisdictions.
To enforce the federal mandate, each jurisdiction needs to have its own law on the books. Currently, four provinces are still without the required legislation or regulations in place to successfully transition their industries to ELDs – British Columbia, Quebec, Nova Scotia and Newfoundland.
CTA believes that governments which are ready with their regulations and legislation should have maintained its position of escalating enforcement starting in June 2022. Waiting for all jurisdictions to be ready, whenever that may be, in the name of ‘national unity’ is not in best interest of public safety or the trucking industry, which has already made the proper investments to comply with the ELD mandate. The vast majority of federally regulated fleets already have ELD technology in their fleets and the three certification bodies approved by Transport Canada and the Standards Council of Canada have qualified multiple ELD offerings, totaling 22 devices from 15 individual ELD vendors.
CTA is adamant Canadians have waited long enough for ELDs, which pave the way for improved highway safety and would also address concerns associated with hours-of-service violations linked to the tragic Humboldt Broncos bus collision, as noted in 2019 by the Saskatchewan Coroners Service.
“ELDs improve safety, fleet and driver performance and are a cost-effective alternative compared to the current paper logbook regime, which is cumbersome, archaic and can be easily falsified,” says CTA president Stephen Laskowski. “There’s simply no reasons pertaining to operations, cost, or safety for trucking fleets and drivers not to be ready for escalated enforcement by June 2022.”
With the announced delay, those provinces that are not yet ready need to prioritize the ELD mandate within their legislative/regulatory process and immediately commit to the industry and the public to begin hard enforcement by January 1, 2023, says CTA. If those four provinces cannot make this guarantee, then the other jurisdictions which are ready by that date must commit to proceeding regardless.
“Without one or both of these commitments, the validity of CCMTA’s January 2023 is in question,” says Laskowski. It’s time for our industry and those provinces ready to enforce the federal ELD mandate to adjust their sails. The regulation is one of the most important road safety measures in the history of the Canadian trucking industry and, by extension, for the motoring public we share our workplace with.
“There should be no more moving the goalposts on dates and no more delays. The time to finally start this important safety regime is past due.”
International Roadcheck Is May 17-19 With a Focus on Wheel Ends
GREENBELT, MD… The Commercial Vehicle Safety Alliance (CVSA) has announced this year’s International Roadcheck dates as May 17-19 with a focus on wheel ends.
International Roadcheck is 72-hour high-visibility, high-volume commercial motor vehicle inspection and enforcement initiative. Commercial motor vehicle inspectors in Canada, Mexico and the U.S. will conduct North American Standard Inspections of commercial motor vehicles and drivers at weigh and inspection stations, on roving patrols, and at temporary inspection sites.
Each year, CVSA focuses on a specific aspect of a roadside inspection. This year, the focus will be on wheel ends. Wheel end components support the heavy loads carried by commercial motor vehicles, maintain stability and control, and are critical for braking. Violations involving wheel end components historically account for about one quarter of the vehicle out-of-service violations discovered during International Roadcheck, and past International Roadcheck data routinely identified wheel end components as a top 10 vehicle violation.
During International Roadcheck, commercial motor vehicle inspectors examine large trucks and motorcoaches and the driver’s documentation and credentials using CVSA’s North American Standard Inspection Program procedures which are the uniform inspection steps, processes and standards established to ensure consistency in compliance, inspections and enforcement. Using the North American Standard Out-of-Service Criteria, also established by CVSA, inspectors identify critical out-of-service violations that if found, require the inspector to restrict the driver or vehicle from travel until those violations or conditions are addressed.
Vehicles that successfully pass a North American Standard Level I or Level V Inspection without any critical vehicle inspection item violations may receive a CVSA decal. In general, a vehicle with a valid CVSA decal will not be re-inspected during the three months while the decal is valid. Instead, inspectors will focus their efforts on vehicles without a valid CVSA decal.
“We want every vehicle on our roadways to be in proper working order for the safety of the driver operating that vehicle and everyone traveling on our roadways,” said CVSA President Capt. John Broers with the South Dakota Highway Patrol.
In consideration of COVID-19 and the health and safety of commercial motor vehicle inspectors and drivers, law enforcement personnel will conduct inspections following their departments’ health and safety protocols during International Roadcheck.
International Roadcheck is a CVSA program with participation by the U.S. Federal Motor Carrier Safety Administration, the Canadian Council of Motor Transport Administrators, Transport Canada, and Mexico’s Ministry of Infrastructure, Communications and Transportation.
Fleet Maintenance and Repair Costs Continue to Increase in Fourth Quarter
Orlando, FL… The American Trucking Associations’ Technology & Maintenance Council and Decisiv Inc., reported that maintenance costs rose 3.7% in the fourth quarter, and are up more than 10% from the previous year.
“The North American economy continues to impact parts and labor costs for fleets in several ways,” said Decisiv President and CEO Dick Hyatt. “However, the ongoing drive to implement more effective and intelligent service management practices among fleet maintenance operations is helping ensure the highest possible levels of equipment utilization.”
The quarterly Decisiv/TMC North American Service Event Benchmark Report was released during TMC’s 2022 Annual Meeting & Transportation Technology Exhibition.
The report found that the average cost of parts and labor for vehicle repairs rose 3.7% in the fourth quarter, driven primarily by increasing labor costs.
From the third quarter to the fourth, labor costs increased 5.4%, while parts cost rose 2.7%. Compared to a year earlier, combined parts and labors costs rose 10.8%. Year-over-year labor costs spiked 14.2%, while parts cost jumped 8.8% from the fourth quarter of 2020 to the final three months of 2021..
The Decisiv/TMC North American Service Event Benchmark Report also shows where fleets spent the largest percentage on maintenance and repairs in Q4 2021 based on VMRS System Level Coding. Topping the list are Power Plant expenses, which accounted for 36.8%, followed by Exhaust systems at 14.9%. Rounding out the top three categories at 5.0% of costs were Brakes.
While the higher percentages of costs associated with Brakes may reflect increased mileage, higher engine and exhaust system related costs could indicate the need to keep vehicles in service longer. Extended trade cycles have become the norm as fleets await production of new and replacement vehicles to return to pre-pandemic levels.
That factor may also be driving some of the increases in parts and labor costs. At the same time, supply chain and inflation issues are likely impacting parts prices. Likewise, higher labor costs are the result of both additional repairs to higher mileage vehicles as well as a reflection of the highly competitive labor market, which requires fleets to increase spending to retain and recruit technicians.
The Decisiv/TMC North American Service Event Benchmark reports are generated using data from the Decisiv SRM platform on service and repair events for more than 7 million commercial assets operating across the U.S. and Canada. The industry’s largest asset service management system is being used to manage a weekly average of 70,000 service events at nearly 5,000 locations.
ATA’s Technology & Maintenance Council issues the reports to its fleet members. The reports are organized based on the Council’s Vehicle Maintenance Reporting Standards sorted by VMRS-coded vehicle systems and geographic location.
TMC fleet members will receive the report electronically via email. For more information on joining TMC, call (703) 838-1763 or visit http://tmc.trucking.org.
OOIDA Response To EPA Cleaner Trucks Announcement
When the Cleaner Trucks Initiative was first announced in 2020, OOIDA stood side-by-side with EPA in hopes that a collaborative rulemaking process with input from professional truck drivers would result in practical emissions standards. Today’s announcement largely ignores that goal in favor of government overreach that will almost assuredly force safe drivers off the road, especially small-business truckers and owner-operators.
Vice President Harris remarked that in Mira Loma, California, commercial trucks made thousands of trips to the town and brought soot, exhaust, and toxic air. She failed to mention anything about all the food, clothes, emergency provisions, and medical supplies that truckers have delivered to American communities throughout the COVID-19 pandemic. The EPA’s proposal highlights the projected millions of fewer lost school days for children, but does not say much about the millions of dollars in equipment and vehicle costs that owner-operators will have to foot the bill for.
Make no mistake, clean air is a priority for everyone. However, we believe there is a more realistic path forward to reducing commercial vehicle emissions that actually involves listening to men and women in the trucking industry. We hope EPA will get back to that strategy as they develop the Final Cleaner Trucks Initiative Rule throughout the rest of the year. Truckers know all too well from experience with previous rulemakings that poorly implemented regulations will result in breakdowns, downtime, and ultimately set back the goal of achieving cleaner air.
Over 140 Local Leaders Ask Pennsylvania Legislature To Oppose Heavier Trucks
HARRISBURG, PA… A group of more than 140 local government leaders in Pennsylvania has signed a joint letter asking the state legislature to oppose any increases in the allowable weight of tractor-trailers on state roads and bridges.
The group, which includes mayors, supervisors, sheriffs and police chiefs, pressed state lawmakers in the wake of the Fern Hollow bridge collapse in Pittsburgh on January 28. Several bills, including H.B. 1232 and H.B. 1559, are pending in the state legislature.
“We have the third largest number of state-owned bridges in the country, with over half over 50 years older,” the officials wrote in the March 8 letter. “More than 3,100 of these bridges have been determined to be in ‘poor condition,’ the same rating assigned to the Fern Hollow bridge.”
“Allowing even heavier trucks than are legal today would only make the current situation worse,” they added.
“Many of us are unable to keep up with our current maintenance schedules and replacement costs because of budget constraints. We do not have the resources to cover the costs of additional infrastructure damage that would be caused by heavier trucks,” they wrote.
The letter, available here, comes as heavier-truck proponents lobby legislators in Harrisburg. Pennsylvania already has more special exemptions for heavier trucks than any state in the country.
Studies have shown that heavier trucks do tremendous damage to roads and bridges. The U.S. Department of Transportation (USDOT) studied truck size and weight and found that thousands of Interstate and other National Highway System bridges would not be able to accommodate longer or heavier trucks, costing billions of dollars in additional bridge costs.
“This is a bipartisan effort to help maintain the safety of our roads and the residents who use them every single day,” said Pittsburgh City Councilman Corey O’Connor. “This is a time when we should be making sensible and strategic investments in our infrastructure, not opening it up to unnecessary wear and tear from vehicles that are heavier than ever.”
Along with infrastructure concerns, Police Chief Scott Bohn (ret.), executive director of the Pennsylvania Association of Chiefs of Police, points to the serious safety risk of heavier trucks to the public.
"Let’s be very clear – heavier trucks are more dangerous trucks,” he said. “Besides the safety issues of collapsing bridges, adding weight increases stopping distance, increases the chance of crashes and can turn minor fender benders into serious injuries and serious injuries into fatalities. Heavier trucks make the public less safe.”
Pennsylvania Facts:
* There were 6,823 large-truck crashes in Pennsylvania in 2019. Unfortunately, 135 people lost their lives in those crashes. (FMCSA, Analysis & Information – Crash Statistics, 2019)
* 3,198 of the 23,166 bridges in Pennsylvania are rated in poor condition, representing 13% of the total bridge stock. (FHWA, Bridge Condition by Highway System, 2021)
* Replacement of bridges rated as being in poor condition in Pennsylvania is projected to be more than $3.6 billion. (USDOT, Bridge Replacement Unit Costs, 2019)
* A total of 51 percent of major roads in Pennsylvania are in poor or mediocre condition, and the effects of these deteriorated roads costs motorists $5.7 billion per year, the equivalent of $639 per motorist. (TRIP, Key Facts about Pennsylvania’s Surface Transportation System, 2022)
Trucking Industry Calls on USDOT to Invest in Nation's Truck Parking Capacity
The American Trucking Associations and the Owner-Operator Independent Drivers Association sent a letter to U.S. Secretary of Transportation Pete Buttigieg urging Infrastructure Investment and Jobs Act funds be prioritized to boost the nation's truck parking capacity. The groups say the nationwide shortage of truck parking has plagued America's truckers for decades, with a wide range of consequences for highway safety, driver health and well-being, supply-chain efficiency, and the environment.
ATA President and CEO Chris Spear had this to say about the issue:
“Washington needs to listen to our nation’s truck drivers and respect their most serious needs. They are the heartbeat of our economy and directly support the frontlines in the fight against COVID—a battle that will only be won with the help of the trucking industry.
“Year after year, surveys show the severe lack of truck parking ranks amongst drivers’ top concerns. More than 98% percent of drivers report problems finding safe parking, burning more than 56 minutes of available drive-time every day to find it. That wasted time amounts to a $5,500 loss in annual compensation—or a 12% pay cut.
“Not only does this add severe strain to the supply chain, but it also presents a growing safety hazard for the entire motoring public. Given the historic levels of funding provided by the Bipartisan Infrastructure Bill, we ask that DOT prioritize this urgent need for America’s truckers.”