Bendix Launches Ad-HFi™ Air Dryer With Electronic Pressure Control Capabilities
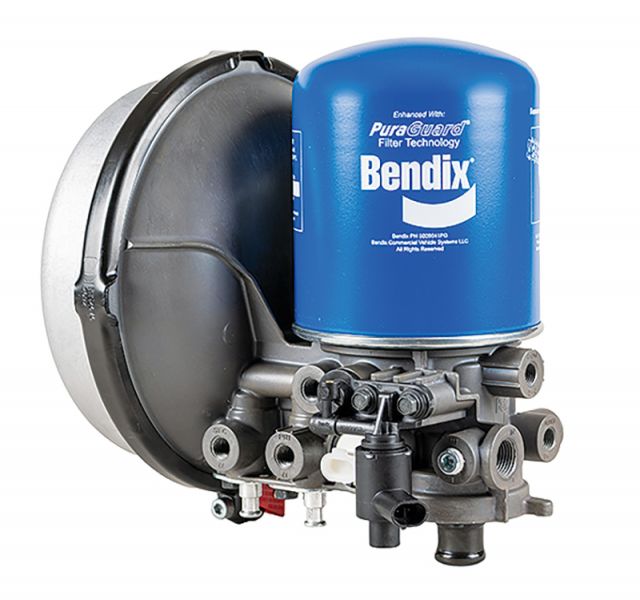
ELYRIA, OH… Consider these three demands of modern full-function air dryer technology: more dry air for the systems today’s trucks depend on; improved energy efficiency; and air system diagnostics. The new Bendix® AD-HFi™ air dryer delivers on all three with the addition of electronic pressure control.
The AD-HFi model features the same leading-edge design of the Bendix® AD-HF® dryer – which Bendix Commercial Vehicle Systems LLC (Bendix) launched in 2019 – but incorporates a solenoid-operated valve that replaces the traditional mechanical governor.
“An electronically controlled governor means we precisely regulate the dryer’s charge and regeneration cycles using Bendix’s Electronic Air Control (EAC) software,” explained Rich Nagel, Bendix director of marketing and customer solutions, Air Supply and Drivetrain. “This function enables the dryer to operate under different parameters in different conditions, increasing its dry air processing capability and saving energy. That same software also provides diagnostics that help fleets and owner-operators get the most out of their dryers and cartridges.”
The AD-HFi is available for order through several major North American commercial vehicle manufacturers.
Mechanical vs. Electronic
With a traditional mechanical governor, a commercial vehicle air dryer has two fixed set-points that determine when the compressor charges and unloads. When the system pressure is fully charged – typically at 130 psi – the mechanical governor sends a pressure signal that tells the compressor to unload. As the vehicle’s brakes are applied – or any other air-driven system uses the compressed air supply – the pressure decreases, and at 110 psi, the governor again signals the compressor to build pressure and recharge the system.
While a mechanical governor’s status operates within two fixed pressure settings, the Bendix® AD-HFi™ air dryer’s solenoid is controlled by Electronic Air Control (EAC) software, which monitors a range of data broadcast across a truck’s J1939 network, including speed, engine torque, and RPM.
“With EAC software, the AD-HFi unit can modify its charge cycle based on air system and engine demands,” Nagel said. “If the software determines that the air system requires extra drying capacity – let’s say you’re hauling multiple trailers or have extra axles, for instance – then it can command additional short purge cycles. This patent-pending technology is called Interrupted Charge Regeneration (ICR). This enhanced purge capability provides significantly more dry air for vehicles that need it.”
Overrun and Overtake
Efficiency and energy savings are also built into the EAC software in the form of Overrun and Overtake functions. When a compressor is building pressure, it consumes approximately 8 to 10 horsepower from the engine. EAC software uses the vehicle’s operating information to determine optimal compressor run times.
“Overrun is when you’re in what we call a ‘favorable energy state,’” Nagel said. “If you’re going downhill or idling, then the engine has ‘free energy,’ which would otherwise be wasted and can now be used for charging. In those situations, the EAC temporarily increases the cut-in and cut-out pressures because the compressor can charge above the standard, programmed pressure without the driver losing engine power.
“Overtake is the opposite: If I’m trying to pass or climbing a hill, then I don’t want the compressor to charge because I need that horsepower. In this case, the EAC lowers the cut-in and cut-out thresholds so the compressor won’t try to build pressure. And ultimately, that’s an energy savings since you’re running the engine more efficiently.” The software is programmed not to reduce the cut-in pressure below a safe setting per FMVSS-121 regulation.
Air System Insights
The EAC software provides air dryer-related status messages over the J1939 network, with the capability to monitor excessive air demand, which can indicate system leaks or other issues. It also monitors regeneration cycles and the amount of air processed during the service life of a dryer cartridge. Using this information along with other data from the compressor, the EAC can signal when it’s time to replace the cartridge.
“Our Electronic Air Control software is loaded with parameters tied to which compressor and engine are on the truck,” Nagel said. “The software is programmed to know what a nominal duty cycle is for that compressor and how much air it should be producing, so it can send a diagnostic code if something isn’t operating correctly. As far as cartridge life goes, it only makes sense that measuring by the amount of air actually processed is better than using mileage as a guideline.”
A message that broadcasts the remaining life of the dryer cartridge can be reset after replacement using Bendix® ACom® Pro™ diagnostic software.
Built on the Best
Like the original Bendix® AD-HF® air dryer, the AD-HFi™ includes field-serviceable, cartridge-style pressure protection valves (PPV) and is designed to work solely with a Bendix® PuraGuard® oil coalescing spin-on cartridge. The PuraGuard cartridge provides the industry’s most effective solution for removing oil aerosols from a compressed air system.
“The difference with PuraGuard oil coalescing is that the oil-coalescing filter media is placed before the air dryer desiccant and uses gravity to remove oil droplets, which gives the cartridge a longer effective life,” Nagel said. “There’s also an internal check valve that prevents the oil removed by the filter from backflowing into the filter media, maintaining the cartridge’s efficiency over its entire duty cycle.”
The quality of a truck’s compressed air supply matters more than ever as commercial vehicles are increasingly equipped with higher levels of automation that incorporate multiple solenoid valves. These valves provide precise control for safety systems and require cleaner air than traditional manual brake valves. Additionally, some Automated Manual Transmissions (AMTs) and emissions equipment rely on pneumatic controls.
“Nobody knows commercial vehicle air treatment like Bendix, and we’ve been pioneering new technologies for decades,” Nagel said. “Trucks change, roads change, technology changes – faster than ever these days – but we’ll keep leading the charge when it comes to air systems that keep vehicles safe and in good operating condition.”
For more information about Bendix air management systems, visit www.bendix.com or call 1-800-AIR-BRAKE (1-800-247-2725). Additional Bendix insight can be found in Bendix’s multimedia center at knowledge-dock.com.